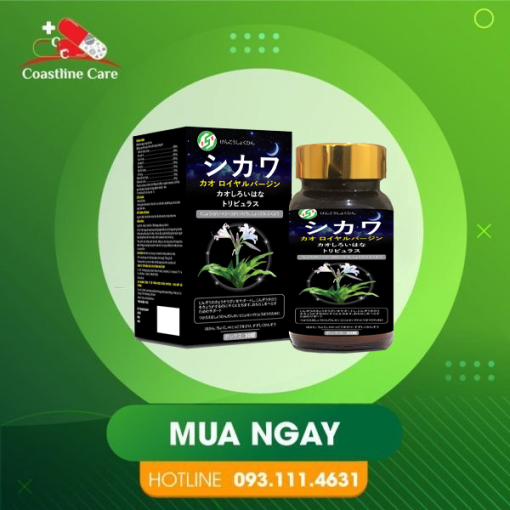
Learn about producing defects, popular leads to, and how manufacturers can implement the most beneficial tactics to avoid faulty solutions.
Also known as a Bring about and Result diagram, or Ishikawa diagram. The tactic was developed by Kaoru Ishikawa during the 1960’s. He made it to assist staff members avoid remedies that basically deal with the signs or symptoms of a much larger dilemma.
You may also use brainstorming methods to determine potential solutions that may handle the root cause of your issue. It is a superb way to get enter from different staff customers and stakeholders.
– exactly where the speculation is evaluated. This could be as simple as measuring an element or as elaborate as developing a new sort of test system.
While in the put up-war era, Japan’s industrial sector was in dire need of rebuilding and modernization. Recognizing the necessity of good quality On this transformation, Ishikawa transitioned to the field of high-quality Regulate. In 1949, he joined the Japanese Union of Scientists and Engineers (JUSE), an organization committed to bettering the quality and performance of Japanese market.
is exactly where the conclusions are acted upon. A speculation may very well be rejected or modified according to new evidence or the outcome of your screening, or simply a program may very well be produced to verify a supported hypothesis.
The Ishikawa diagram was created by Kaoru Ishikawa over the nineteen sixties as being a technique for measuring good quality Manage procedures inside the shipbuilding business.
An Ishikawa (or fishbone) diagram really should be developed after the challenge statement is penned and info is gathered. An Ishikawa diagram should be seen like a graphical depiction of hypotheses that could clarify the failure below investigation.
Sorting prospective will cause into unique types makes it simpler to identify root causes later on. You should use the 6Ms as a starting point that will help you choose vital styles.
Esas líneas permiten analizar las causas principales nha thuoc tay y las secundarias con un gran nivel de detalle e incluir elementos que no se consideraban pertinentes o relevantes, pero que pueden ser la verdadera razón de un problema.
Veja alguns benefícios de realizar uma análise da causa raiz usando a metodologia de causa e efeito no diagrama de Ishikawa:Encontre facilmente a causa raiz. Um diagrama de Ishikawa é uma ferramenta visual que acrescenta estrutura e clareza à solução de problemas. Ele indica o problema e suas possíveis causas em um único local, tornando mais fácil nha thuoc tay para as equipes encontrar a causa raiz do problema. Previne problemas adicionais. Ao encontrar a causa raiz do problema, você corrige o problema em sua fonte e mitiga problemas futuros.
Una de las primeras contribuciones de Kaoru Ishikawa a nha thuoc tay la Calidad fue la difusión del Círculo de Calidad, un concepto que creó junto con otros miembros de JUSE.
Durch die Identifizierung der wichtigsten Bereiche und der möglichen Ursachen kann so leichter eine Lösung gefunden werden.
Lọ viên tiểu đêm Shikawa Viên uống Shikawa Nhật Bản hỗ trợ bảo vệ sức khỏe liên quan đến các vấn đề về thận và bàng quang như: